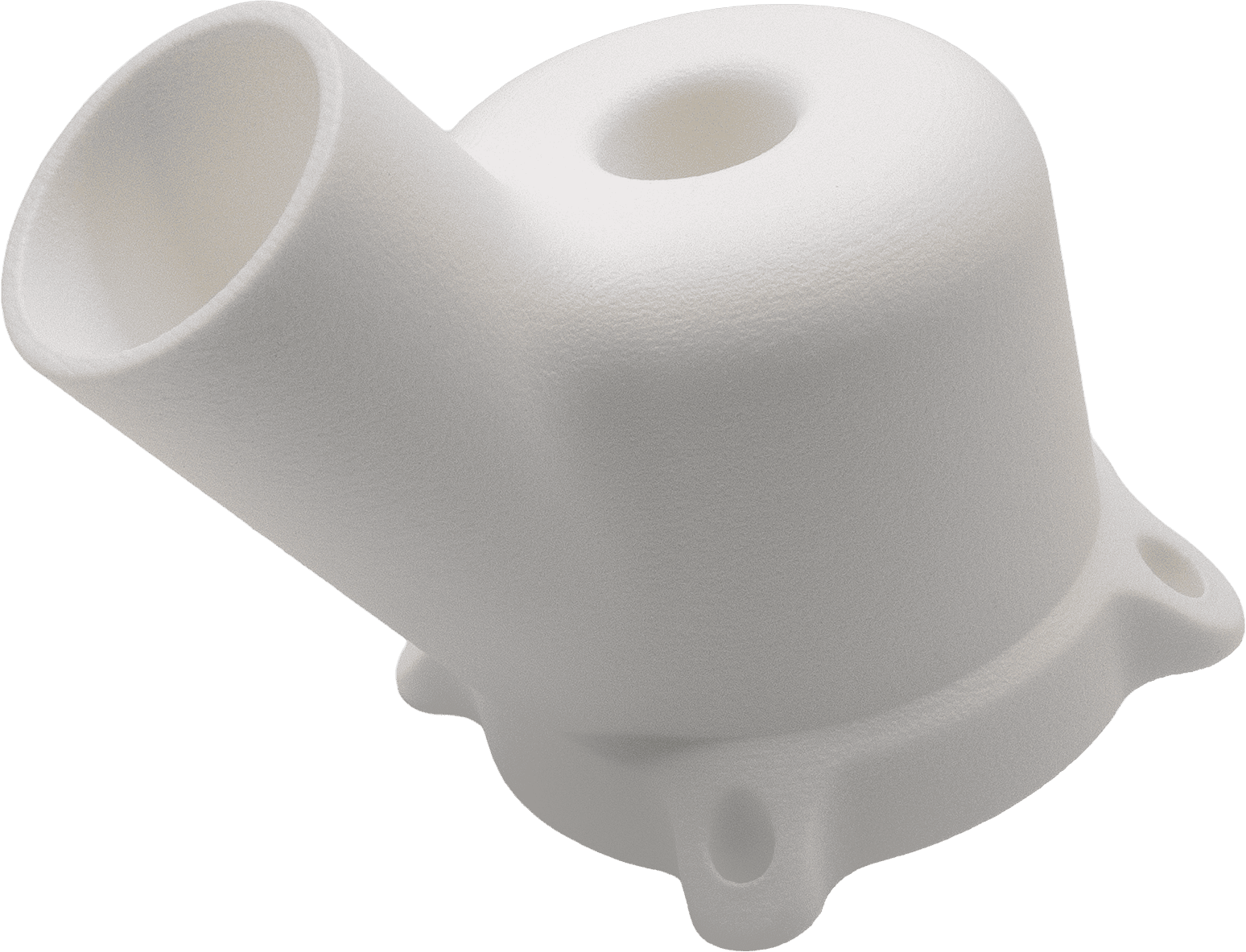
Präzise & flexibel für Kunststoffbauteile.
Selektives Lasersintern Technologie (SLS)
Selektives Lasersintern nutzt Lasertechnologie zur Herstellung komplexer Teile – ideal für Prototypen, Kleinserien und individualisierte Produkte.
Präzise & flexibel für Kunststoffbauteile.
Selektives Lasersintern nutzt Lasertechnologie zur Herstellung komplexer Teile – ideal für Prototypen, Kleinserien und individualisierte Produkte.
Sie sind hier:
Startseite » 3D Druck Service » Technologien » Selektives Lasersintern (SLS)
Bei der SLS Technologie arbeitet man mit einem feinen Kunststoffpulver das als Ausgangsmaterial dient. Bei diesem Kunststoffpulver handelt es sich meist um Nylon. Es wird zu Beginn des Druckprozesses mit einer Rakel in einer dünnen Schicht (80-150 µm) auf der Bauplattform aufgetragen. Diese Plattform lässt sich in einem sog. Bauzylinder in kleinen Abstufungen absenken.
Die 3D Daten für den Druck müssen zu Beginn ebenso in dünne Schichten zerlegt werden. Diese digitale Vorbereitung übernimmt eine sog. Slicing-Software. Danach werden die vorbereitet Daten auf die SLS Maschine geladen und der Druck kann beginnen.
Beim Lasersintern wird, wie der Name schon vermuten lässt, ein Laserstrahl für das Verschmelzen des feinen Pulvers verwendet. Die durch die Rakel vorbereitete Pulverschichten werden nun mit den vorbereiteten Daten belichtet. Jede dünne Datenschicht wird so auf die jeweilige Pulverschicht durch den Laser projiziert. In dem oben gezeigten Video ist der beschriebene Prozess sehr gut zu erkennen. Sobald eine Schicht abgeschlossen ist, senkt sich die Bauplattform in dem Zylinder um die jeweilige Schichtstärke ab.
Der Bauraum eines SLS 3D-Druckers wird während des gesamten Druckprozess beheizt. Diese thermische Energie muss nach dem Drucken wieder entweichen. Dabei kühlt der Baujob zuerst noch für ein paar Stunden in der Anlage selbst bis auf eine moderate Temperatur ab. Danach wird der Bauraum aus der Anlage herausgenommen und muss bei Raumtemperatur weiter abkühlen. Dieser Vorgang muss so schonend (langsam) wie möglich erfolgen da sonst ein Verzug an den SLS Bauteilen auftreten kann.
Nach der Abkühlphase können die gesinterten Bauteile aus dem Baujob herausgenommen werden. Dabei kann das meiste lose nicht gedruckte Pulver sehr einfach per Hand bzw. mit Pinseln entfernt werden. Eine dünne Schicht backt jedoch ganz leicht an den SLS Teilen an, welches dann final durch Glaskugelstrahlen entfernt werden kann.
Sie sind hier:
Startseite » 3D Druck Service » Technologien » Selektives Lasersintern (SLS)